An Introduction to LVL Construction: Strength, Stability, and Safety
In the world of construction, the materials used play a critical role in the durability, safety, and overall quality of structures. One such material that has gained immense popularity is Laminated Veneer Lumber (LVL). This engineered wood product has become a staple in modern construction due to its strength, stability, and flexibility. In this article, we will explore the fundamentals of LVL construction, its benefits, and its future in the building industry.
Understanding LVL Construction
LVL construction refers to the method of using laminated veneer lumber, which consists of thin layers of wood veneer glued together to create a more robust and usable product. The process involves taking high-quality veneers, stacking them together, and bonding them under heat and pressure to enhance their properties. This engineered wood alternative is particularly beneficial in various construction applications, offering both aesthetic appeal and structural integrity.
The Basics of LVL Construction
The fundamental concept of LVL construction revolves around the use of wood fibers. By orienting these fibers in the same direction during manufacture, LVL achieves superior bending strength and stiffness, making it an ideal choice for beams, headers, and other structural applications. Unlike traditional lumber, LVL is manufactured with controlled conditions, reducing natural flaws such as knots and warping that can compromise quality.
One of the standout features of LVL is its versatility; it can be cut and shaped to fit specific design requirements, allowing architects and builders to fully explore their creativity. This adaptability is a significant factor that makes LVL a favored material in both residential and commercial building projects. Furthermore, LVL can be engineered to meet specific load requirements, making it suitable for a wide range of applications, from large-scale commercial buildings to intricate residential designs. Its lightweight nature also simplifies transportation and installation, further enhancing its appeal in the construction industry.
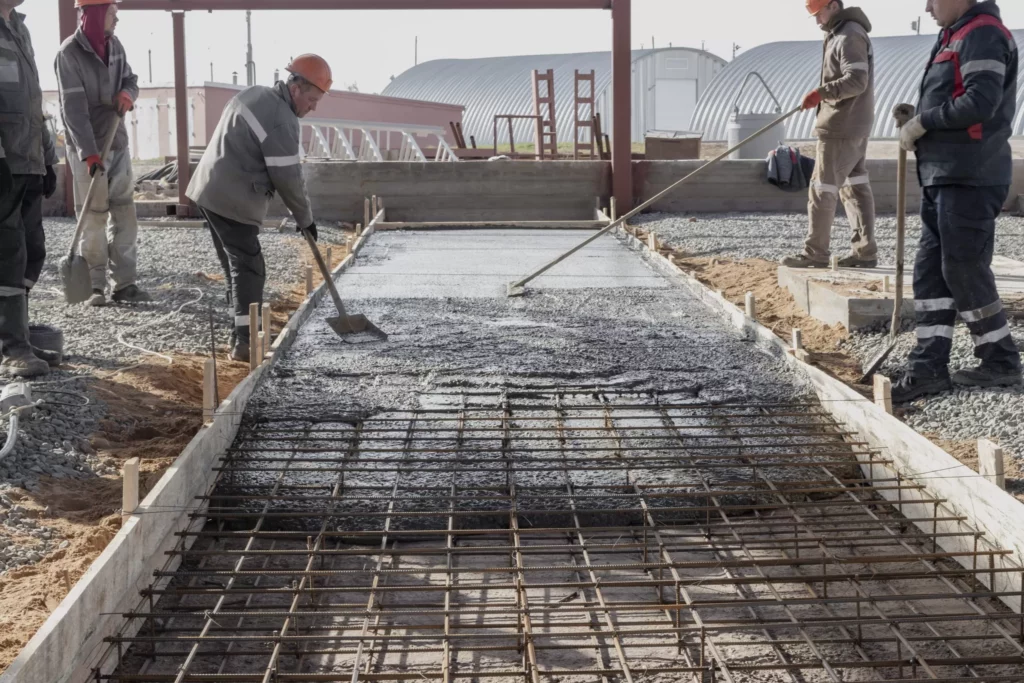
Key Components in LVL Construction
Several key components contribute to the efficacy of LVL construction. Firstly, the wood veneers used must be of high quality, as lower-quality materials can result in a weaker final product. Secondly, the adhesives employed in the process are crucial. They must provide strong bonding while maintaining flexibility to allow the wood to flex under stress without breaking. Lastly, the manufacturing process itself must adhere to stringent standards to ensure product reliability and safety.
Other components include protective treatments, which can enhance resistance to moisture, bugs, and decay, ensuring the longevity of LVL structures. Understanding these components is essential for anyone involved in construction or renovation projects. Additionally, the environmental impact of LVL construction is noteworthy; as it is made from renewable resources, it can be a more sustainable choice compared to traditional building materials. Many manufacturers source their veneers from responsibly managed forests, contributing to a reduced carbon footprint and promoting sustainable forestry practices. This eco-friendly aspect is increasingly important to builders and homeowners alike, as they seek to minimize their environmental impact while still achieving high-quality construction results.
The Strength of LVL Construction
When it comes to construction materials, strength is paramount. LVL excels in this department and is consistently tested against other materials to reaffirm its position in the market. Not only does it support substantial loads, but it also resists bending and warping, making it ideal for a variety of applications.
Factors Contributing to LVL Strength
The strength of LVL construction is influenced by several factors. The quality of the wood veneers is the most significant factor, with straight grains and minimal defects providing enhanced strength. The pressing method used to laminate the layers also plays a crucial role. A high-pressure process ensures the layers bond tightly, increasing overall strength. Additionally, the adhesive’s properties, including its curing time and moisture resistance, contribute significantly to the durability and strength of LVL.
Furthermore, the layering technique allows for uniform distribution of stress across the entire beam, minimizing weak points that could compromise structural integrity. This engineered approach to construction results in materials that outperform standard lumber in most applications. The controlled manufacturing process also means that LVL can be produced to specific dimensions and performance characteristics, allowing architects and builders to design structures that meet exact specifications without sacrificing strength or safety. Read more about integrity at https://online.hbs.edu/blog/post/what-is-data-integrity
Comparing LVL Strength with Other Materials
To fully appreciate the robustness of LVL, it is essential to compare its strength against traditional materials such as solid wood and steel. While solid wood can be strong, its natural qualities may lead to inconsistencies. In contrast, LVL offers uniform strength, making it a preferred option for many engineers. The predictability of LVL’s performance under load is a significant advantage, particularly in applications where safety and reliability are critical, such as in large commercial buildings and bridges.
Though steel has high tensile strength, its heavy weight can complicate transportation and installation. LVL, being significantly lighter, provides a practical alternative, allowing for easier handling and lower shipping costs. This lightweight nature also reduces the overall load on foundations, which can lead to cost savings in excavation and concrete work. Ultimately, LVL combines the best features of various materials, making it a versatile choice in modern construction. Its adaptability extends beyond structural applications, as LVL is increasingly being used in innovative designs, including curved and complex shapes that would be challenging to achieve with traditional materials.
Stability in LVL Construction
Another essential aspect of LVL construction is stability. In construction, stability refers to the ability of a material to maintain its shape and dimensions under stress or environmental changes. LVL is designed to offer superior stability, mitigating issues often associated with natural wood products.
How LVL Provides Stability
One of the primary reasons LVL exhibits such stability is its engineered nature. During production, moisture content is carefully monitored and controlled. This minimizes the risk of warping or splitting due to fluctuations in humidity or temperature. Additionally, the layers are bonded tightly, preventing the internal movement of the wood fibers that can lead to instability.
Moreover, the arrangement of the veneer layers ensures that any potential flexing occurs along predetermined areas, further contributing to enhanced stability. This engineered product can perform reliably in environments exposed to varying conditions, making it perfect for regions that experience drastic climate changes. The consistent quality of LVL also means that builders can predict its performance with greater accuracy than traditional lumber, leading to more efficient design and construction processes.
Stability Considerations in LVL Construction
When utilizing LVL in construction, it’s vital to consider various stability-related factors. The design and width of the beams, their load-bearing roles, and their placement in structures can significantly influence overall stability. Engineers must calculate the necessary specifications carefully to optimize performance. This includes understanding the load distribution across the beams and ensuring that the connections between different structural elements are robust enough to handle the stresses involved.
Additionally, while LVL is known for its stability, it is still important to incorporate proper support systems, like bracing, in larger structures. This proactive approach enhances stability and significantly improves safety during the construction process and throughout the life of the structure. Furthermore, LVL’s compatibility with other materials, such as steel and concrete, allows for innovative hybrid designs that can further enhance stability and resilience against environmental factors. The versatility of LVL in various applications, from residential homes to commercial buildings, showcases its critical role in modern construction practices. Click here to find more about environmental.
Safety Aspects of LVL Construction
The safety of a structure is a fundamental concern for architects, engineers, and builders alike. LVL construction features several safety characteristics that contribute to a safer building environment.
Safety Measures in LVL Construction
One of the most significant safety measures associated with LVL is its resistance to warping and splitting. As mentioned earlier, the controlled manufacturing process limits natural defects that can lead to structural failure. LVL’s predictable performance under load contributes to a higher safety factor in any construction project, allowing builders to design structures with confidence.
Additionally, LVL can be treated for fire resistance, further enhancing safety. Special coatings and treatments can reduce the risk of combustion, making LVL a viable option in areas where fire risk is a concern. This fire-resistant capability is particularly important in urban environments where buildings are in close proximity, as it helps to mitigate the spread of fire from one structure to another, thereby protecting lives and property.
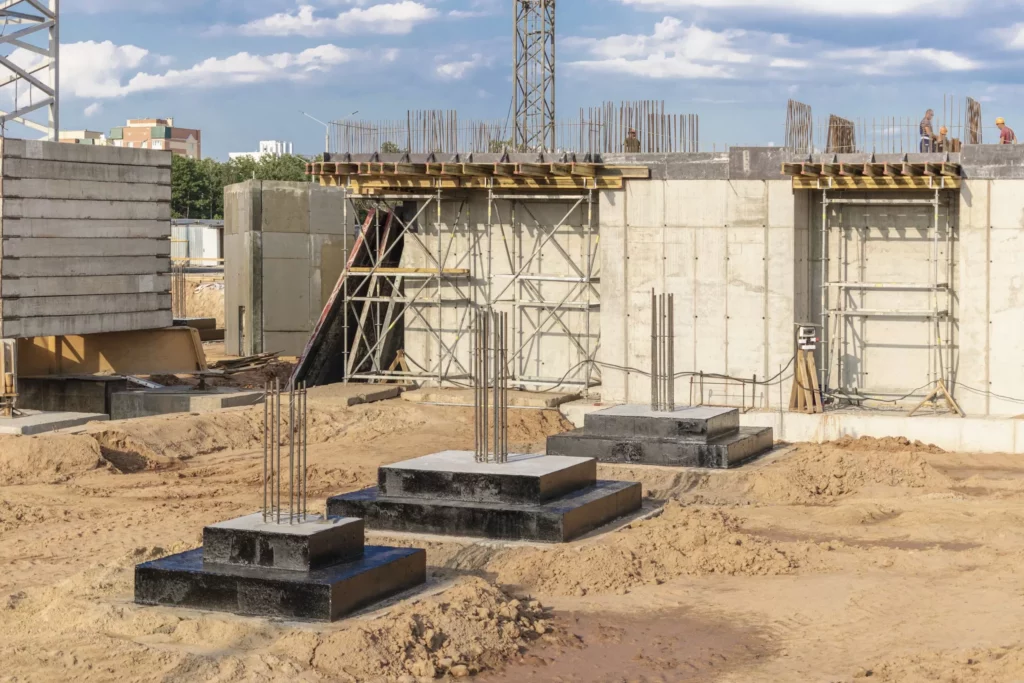
Ensuring Safety in LVL Construction Projects
To ensure safety when incorporating LVL into construction projects, engineers and project managers should adhere to building codes and industry standards. Regular inspections during the manufacturing and construction phases can spot potential issues early and prevent costly mistakes. These inspections not only help maintain quality control but also ensure that the materials used meet the required safety specifications, which is essential for the integrity of the overall structure.
Training for construction teams on the proper handling and installation of LVL products is also crucial. This enhances understanding of the material’s capabilities and limits, leading to a safer working environment for all involved in the construction process. Furthermore, implementing a robust safety protocol that includes personal protective equipment (PPE) and emergency response plans can significantly reduce the risk of accidents on-site. By fostering a culture of safety, teams can work more efficiently and effectively, ultimately contributing to the success of the project while prioritizing the well-being of everyone involved.
The Future of LVL Construction
The future of LVL construction looks promising, with ongoing advancements in technology and materials science driving innovation in engineered wood products. As the demand for sustainable building materials increases, LVL stands out as a carbon-friendly choice that contributes to reducing the construction industry’s overall carbon footprint.
Innovations in LVL Construction
Recent innovations in LVL manufacturing processes are resulting in even stronger and more versatile products. Companies are continuously researching new adhesives, wood species, and layering techniques to enhance LVL’s performance and expand its applications. This innovation allows for the creation of larger spans and unique architectural features that were previously unattainable with traditional materials.
Additionally, automation in manufacturing processes is increasing efficiency and consistency in LVL production, further improving its reliability as a construction material.
Sustainability and LVL Construction
As environmental concerns become increasingly urgent, sustainability is at the forefront of construction strategies. LVL offers a resource-efficient alternative to traditional construction materials, as it utilizes fast-growing timber species and maximizes the use of forest resources. This aligns with modern ecological practices aimed at promoting responsible timber sourcing.
Moreover, because LVL is manufactured from renewable resources, its use can significantly lower the overall carbon footprint of a building. As architects and builders pursue sustainable building practices, LVL will continue to be a key component in creating environmentally friendly structures.
In conclusion, LVL construction presents a compelling option for those seeking strength, stability, and safety in building materials. As this engineered wood product continues to evolve, it holds the potential to reshape the future of the construction industry, paving the way for more resilient, sustainable, and innovative building practices.
Other resources: Where to Buy LVL Timber for Professional Formwork Applications